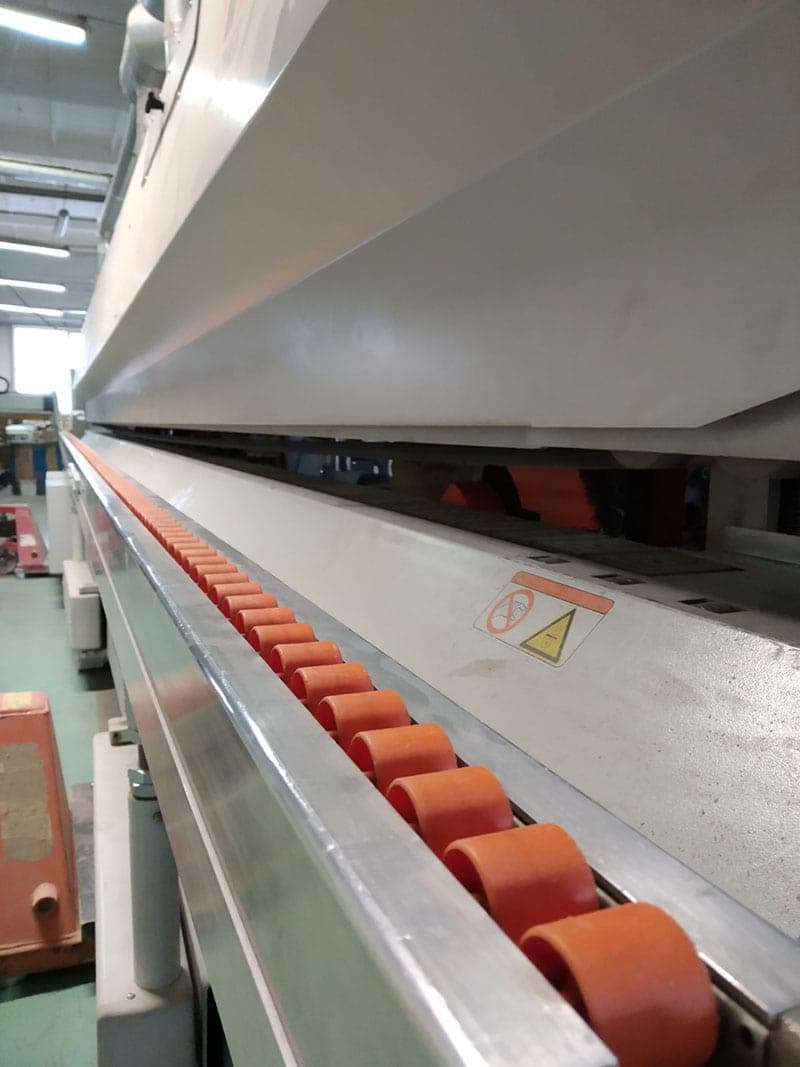
Manufacturing process at our company
at our company
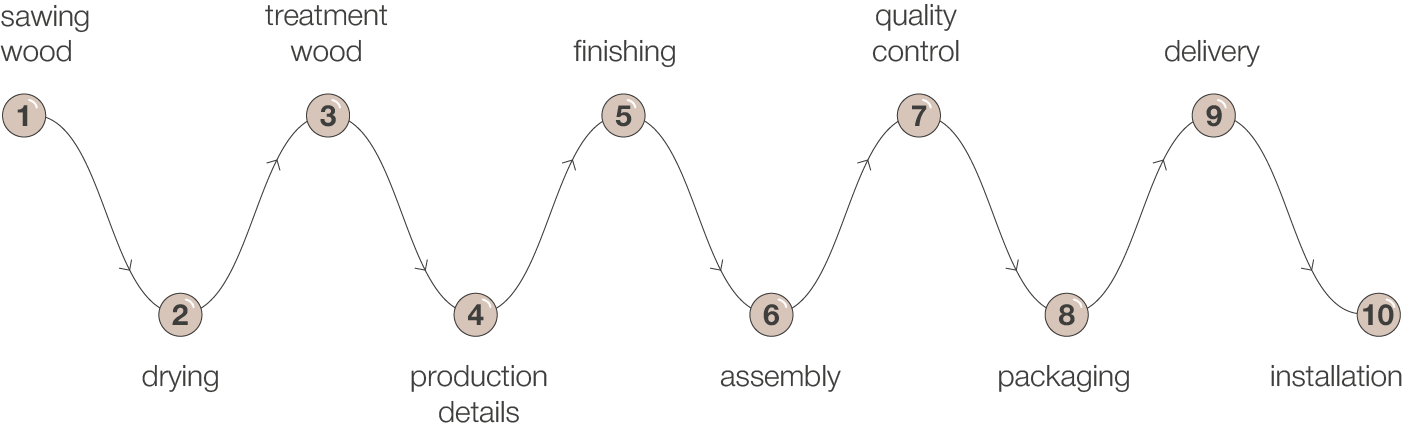
In order to facilitate installation, we pre-assemble our furniture:
- cabinet carcasses come pre-assembled;
- cornices and plinths require minimum adjustment;
-pre-drilling for easy hardware installation.
- cabinet carcasses come pre-assembled;
- cornices and plinths require minimum adjustment;
-pre-drilling for easy hardware installation.
30 years
Experience
Experience
over 190
Employees
Employees
Sawing timber
We have our own sawing machines. . We do not buy lumber, instead we process wood according to our specific needs and requirements.
On-site
sawing
sawing
=
reduced
costs
costs
We dry wood at the factory. We use INCOPLAN wood drying equipment for high quality drying, which guarantees our furniture will look unchanged and function properly for many years. The multistage drying process brings the moisture content to the optimum without swelling or cracking.
7-9%
moisture content in the wood
moisture content in the wood
Up to 30 days
wood drying
wood drying
140 cubic meters
volume of wood dryer loading
volume of wood dryer loading
Milling
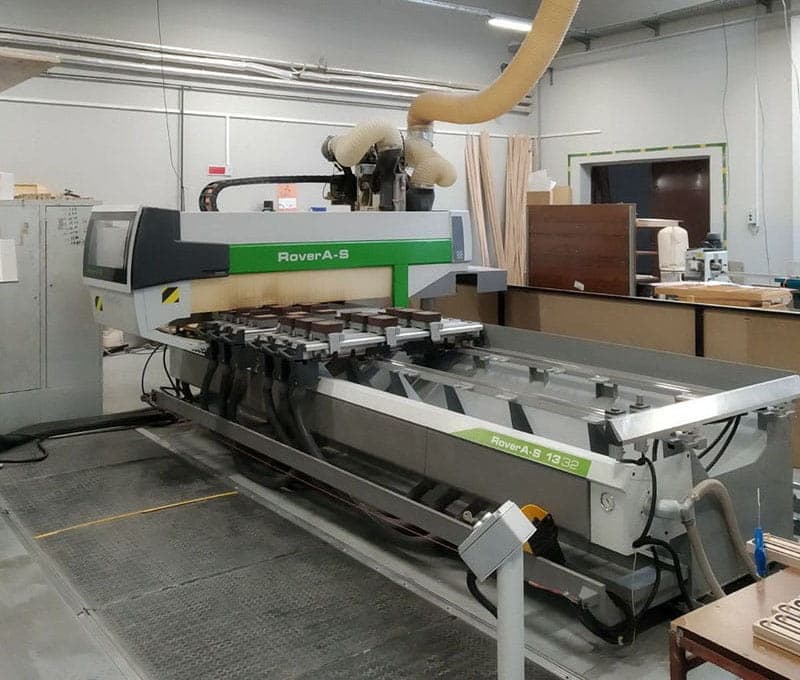
We have
several CNC processing centers made by Biesse, Italy. We use them to perform computer-controlled drilling and shaping operations with extreme precision.
Door edge
processing
Geometric accuracy of machined elements - up to 0.1 mm
processing
Geometric accuracy of machined elements - up to 0.1 mm
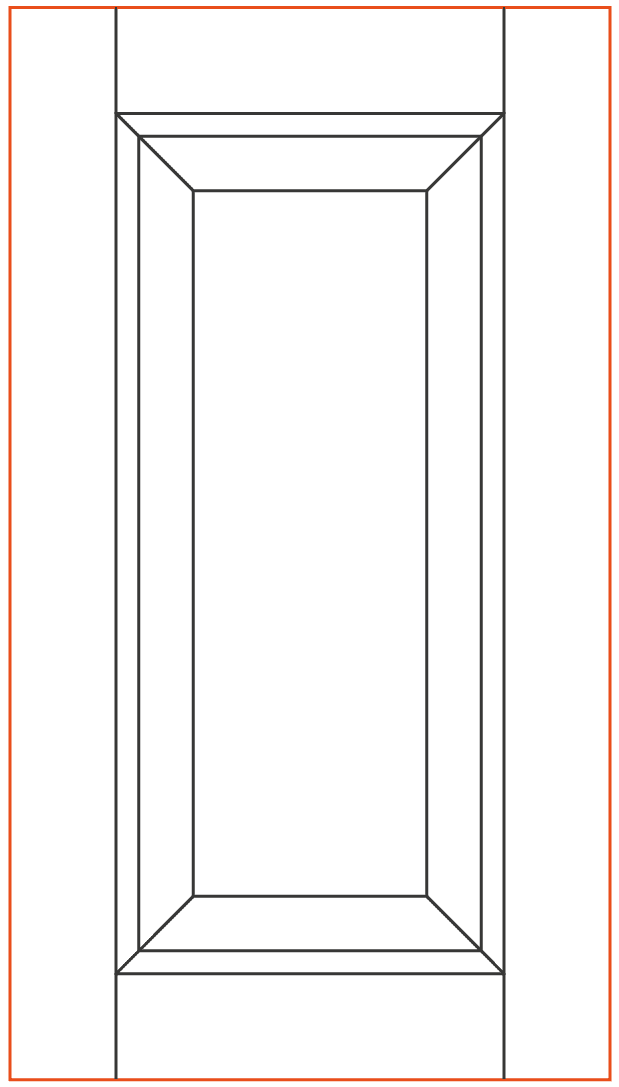
Milling decorative
elements
curvilinear parts, pilasters, etc
elements
curvilinear parts, pilasters, etc
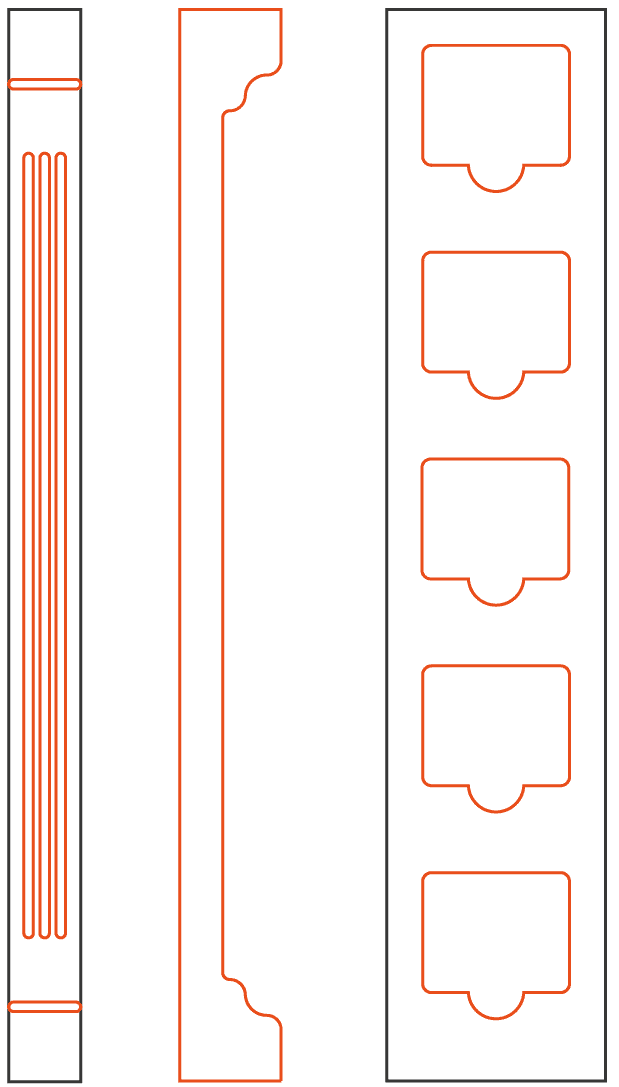
Nesting and cutting flat material
In order to make cabinet panels and slab doors, we cut laminate, Wood veneer, MDF, plastic and acrylic flat material by means
of Selco cutting machines from Biesse, Italy.
Automated material processing
reduced operating time; accurate dimensioning - accurate assembly
Optimum nesting
reduced costs of end products
1
Automated material processing
reduced operating time; accurate dimensioning - accurate assembly
2
Optimum nesting
reduced costs of end products